We sell phosphors for plasma and neon artists! To purchase phosphors, CONTACT US with your order.
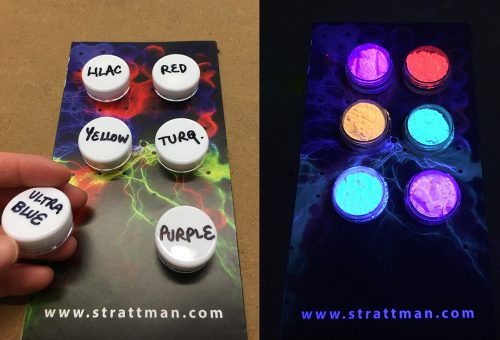
Sample pack of six phosphor colors.
***Please specify if you want specific colors in your sample pack***
These are small 3g size sample jars with screw-on lid. (The weight of different colored phosphors can vary, but it will be a full sample container of each color). These sample sizes of phosphors can go a long way, since often only a small amount is needed to coat a tube.
We recommend crushing the phosphor into a fine powder before use. For tips on using phosphors and additional information, see the FAQs at the bottom of this page.
Phosphor colors can also be purchased individually, in 50 gram or 100 gram quantities. The phosphors are sold as a dry powder; you can mix it with a binder or alcohol as needed (see usage information below).
*Phosphors in the color chart are photographed under UV light to show the color as accurately as possible the way it will look inside a plasma/neon tube. The brightness of the color may depend on your application technique. For questions about the appearance of specific colors, contact us and we may be able to provide additional examples of the effects.

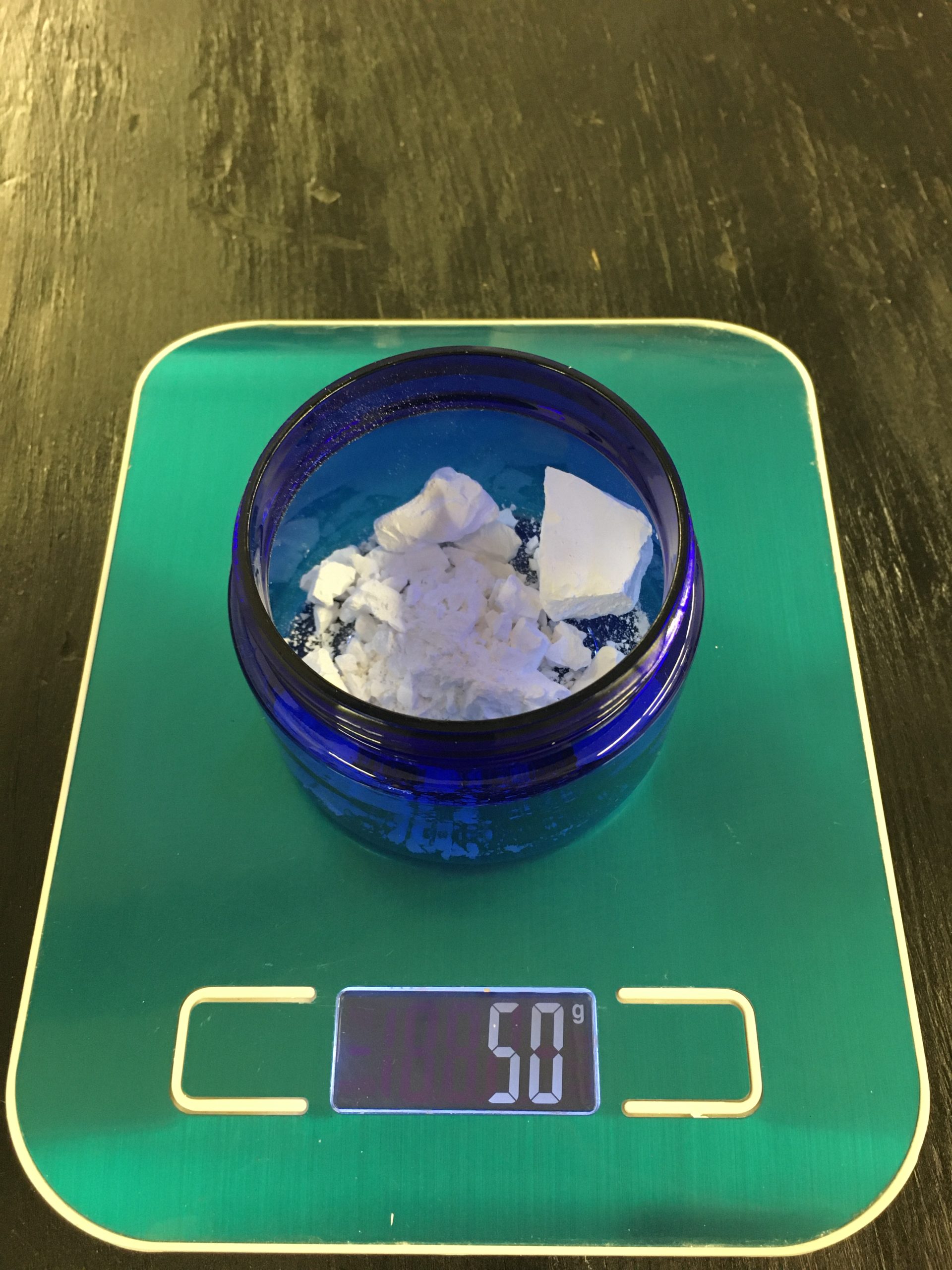
50 gram amount
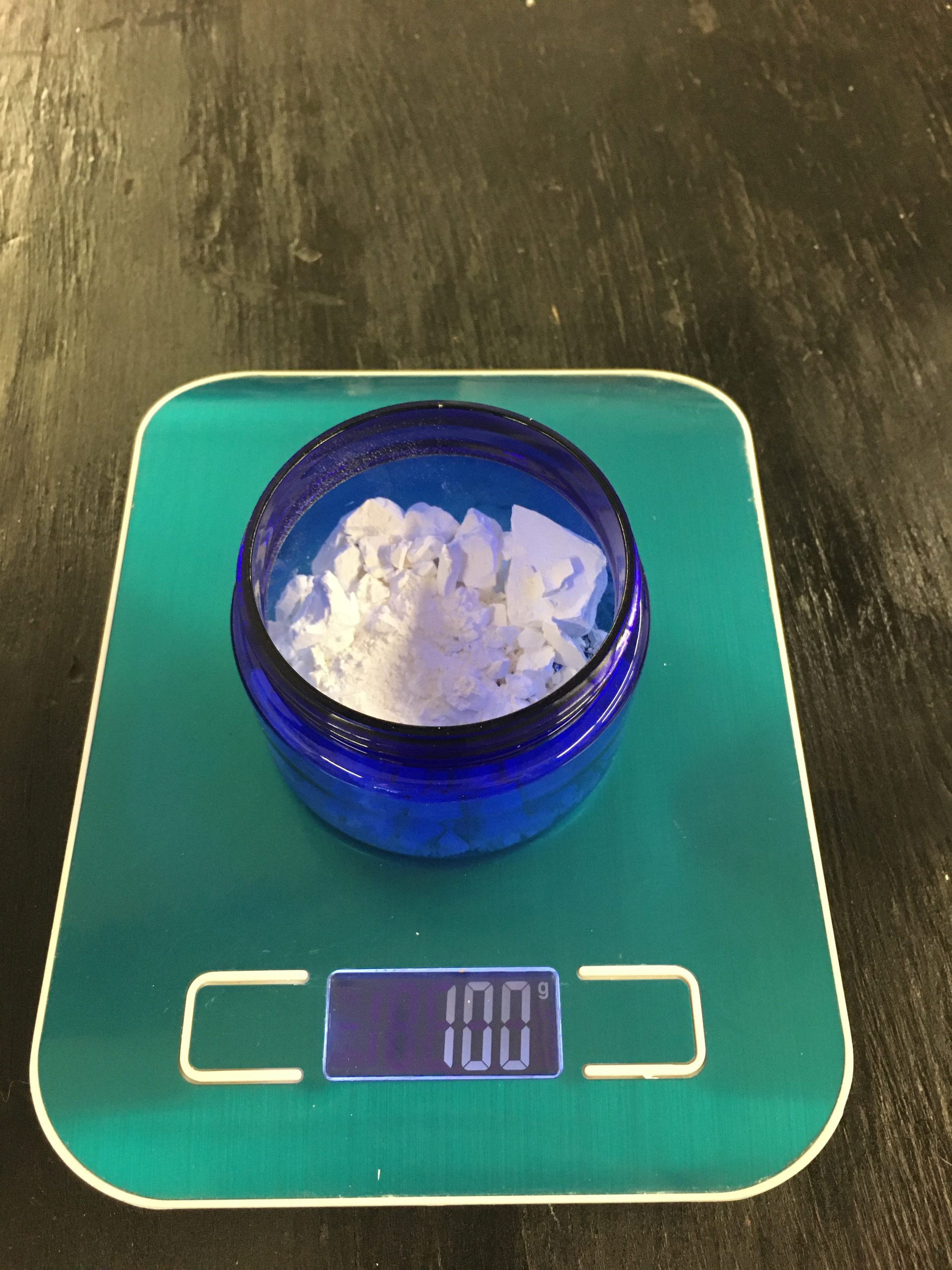
100 gram amount
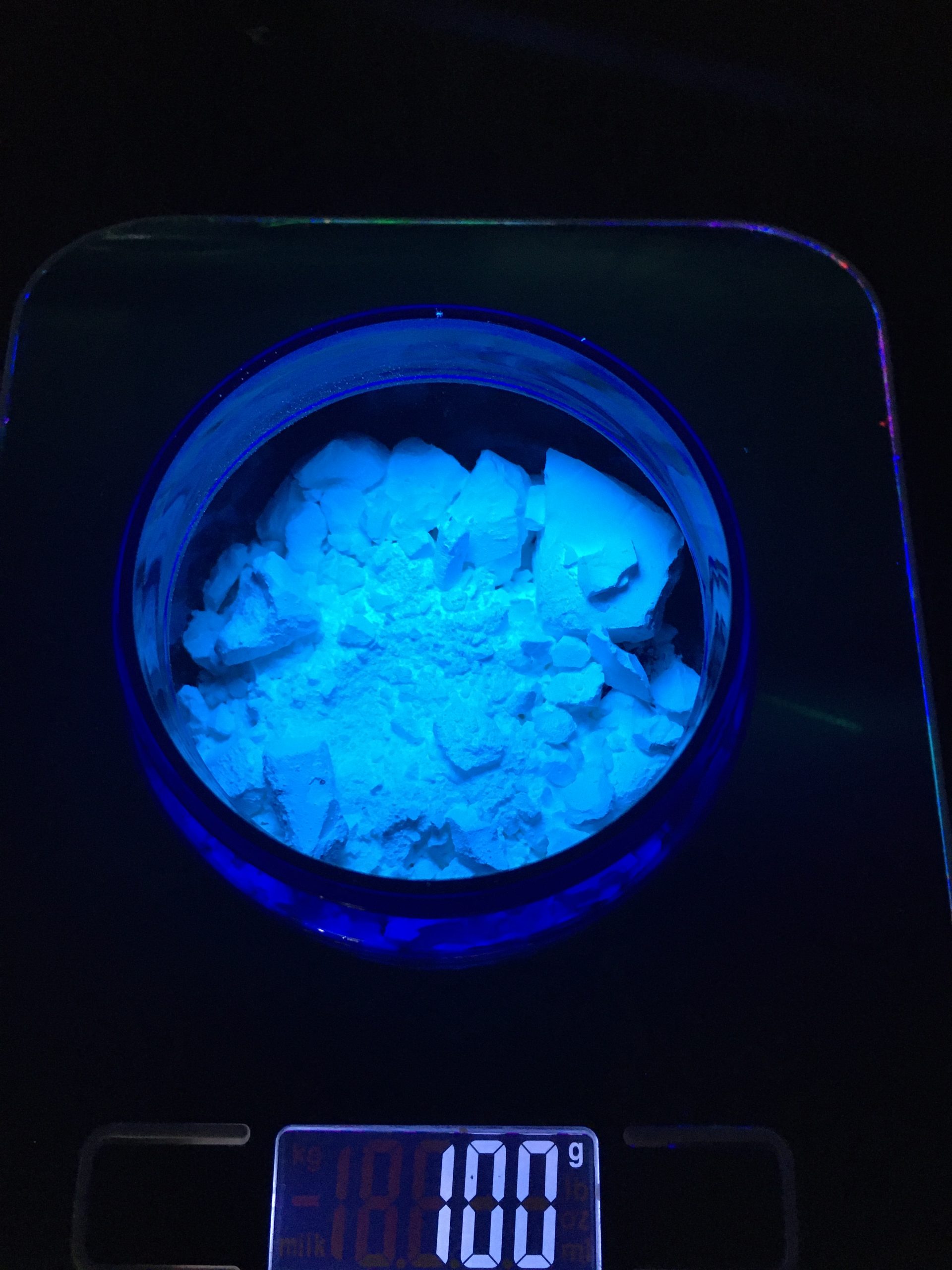
Example of 100 grams blue phosphor under UV light
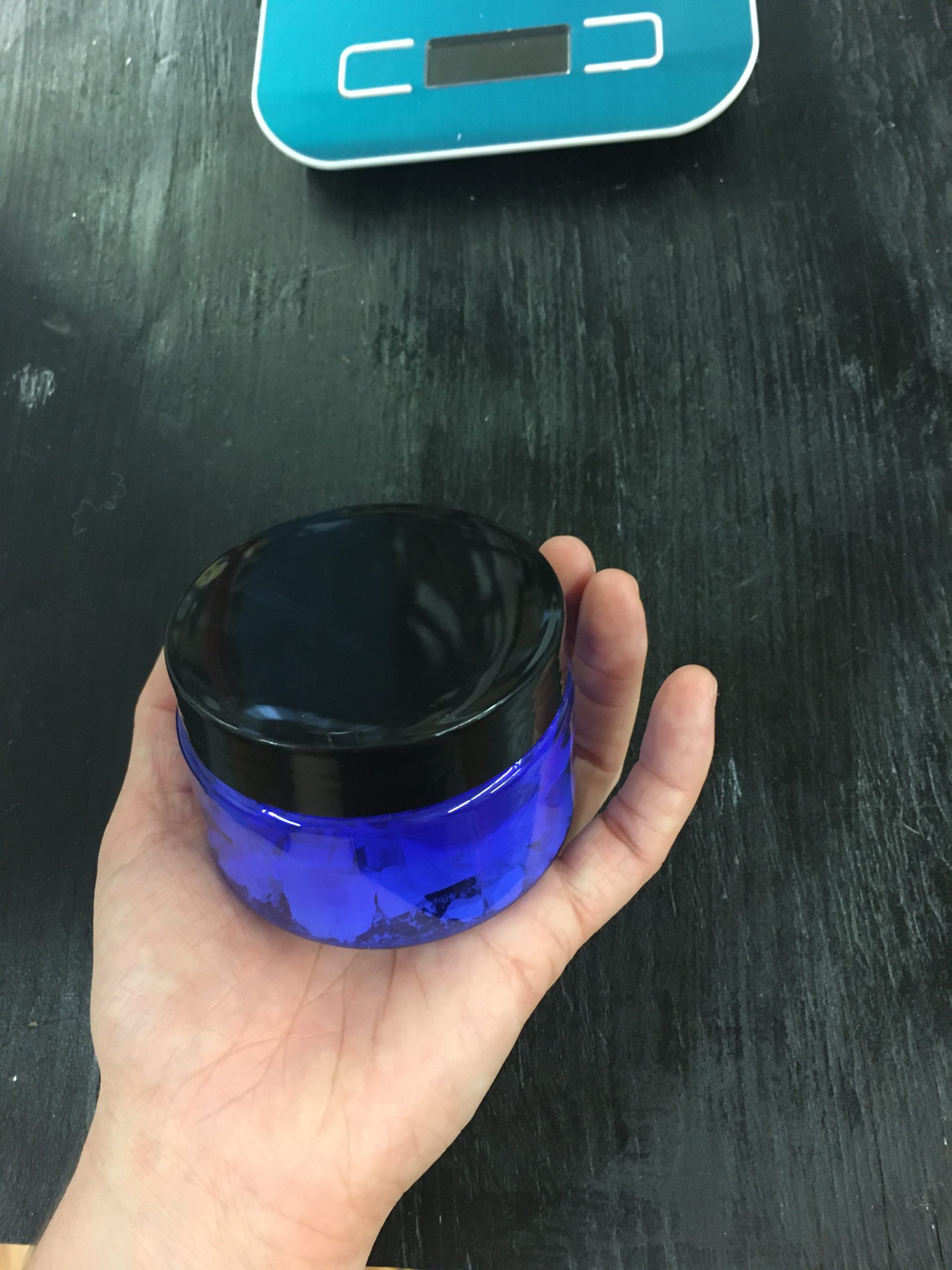
*jar size may vary and may not be full; phosphors are measured by weight in grams
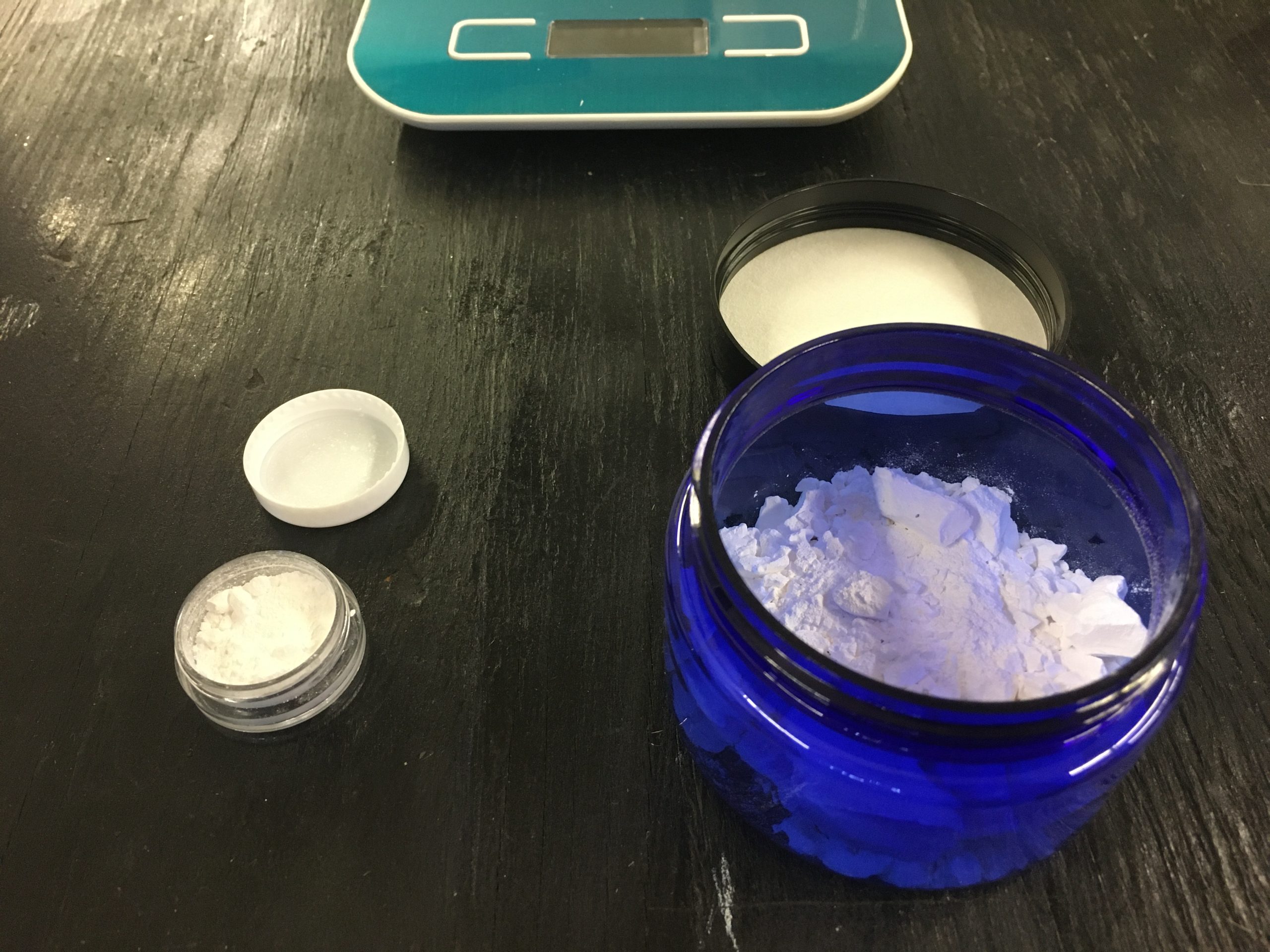
Sample size (left) / 50 or 100 gram jar (right)
Phosphors: Frequently Asked Questions
***For even more comprehensive information on the use of phosphors, see Wayne Strattman’s new book The Art of Plasma. Chapter 4 covers Plasma Gases, Vapors, Phosphors and Metals in the Tube.***
An overview of phosphor usage and techniques:
1. What is a phosphor?
A phosphor is a photoluminescent material that absorbs energy from the shorter wavelengths of light, often in or near the ultraviolet range. The phosphor then reemits this energy in a longer-wavelength part of the spectrum—namely, visible light. Phosphors are used in gas discharge tubes to produce colorful glowing effects. Inert gases produce UV plasma light (some more than others) that excites the phosphors.
Phosphors were first developed in the 19th century when various natural elements were put in Geissler tubes. After the air was partially evacuated and under the action of a high voltage discharge the elements would glow. The ultraviolet light produced caused the rocks to fluoresce. When powdered these rocks became our first phosphors.
An example of a Crookes Tube containing four fluorescent and phosphorescent minerals. Image courtesy of SPARK Museum of Electrical Invention
Phosphor technology research progressed through the last century and continues to advance rapidly today. Now, a rainbow of colors is available.
Phosphors have many technical properties and requirements that fill textbooks but here are some basic tips and techniques for the plasma artist.
2. How are phosphors used in gas discharge tubes?
In the form of powders (sometimes mixed with a binder or alcohol), phosphors can be applied to the inner surface of the tube in many different ways. Phosphors can be used in 2 basic modes:
- Reflective mode: This means the UV light from the plasma discharge impinges on an internal surface which results in it reflecting a visible light. An example of this is if a sculpture is mounted inside a clear glass envelope containing the plasma. The inner sculpture is coated with phosphor and would reflect colored light. This mode produces the brightest light and brilliant colors. The gas discharge itself will also add its own characteristic body color.
- Transmissive mode: This is what happens in a neon or fluorescent tube. The UV light hits the coating from the backside and transmits visible light which passes through the coating. This method requires careful control of the coating thickness and uniformity or all that will result is a muddy look due to too thick a coating.
Different kinds of phosphors have different particle sizes. (There is no visible difference with such small particle sizes but it makes a difference when choosing the best method of application.)
- Larger particles, for example >5 microns and up, usually require a binder to make the particles adhere to the glass. This method will provide an evenly coat of phosphor. The binder must be able to be cleanly burned off in the presence of air (or at least oxygen) at elevated temperatures. Failure to thoroughly burn this off will lead to reducing the binder to carbon, blackening the glass.
- Phosphors milled to <1 micron do not require the use of a binder; they can be applied with just an alcohol vehicle which will quickly dry leaving a thin coating that readily adheres to the glass. (It will work best to use 100% isopropyl alcohol with no water in it.) Larger particle size may require binder to stick.
- The traditional binder for phosphors was nitrocellulose. Currently polyethylene oxide (trade name Polyox) has replaced this.
- Various particle sizes may work with the sand application method.
3. How should phosphors be applied to glass?
There are several common ways to apply phosphors to glass. (Note that phosphors should be finely ground to powder using a mortar and pestle before using any of these methods. Even if they are already in powder form, this can separate into clumps over time so it is best to finely grind the phosphor as needed, either before mixing with a liquid vehicle or before applying as a dry dust coating.)
- Pouring: For a uniform coating on a tubular shape, fill it with a slurry of phosphor and a liquid binder, such as polyethylene oxide or the older nitrocellulose solution, and allow it to drain into a reservoir. The tube is then allowed to dry with a gentle stream of air. If a chemical binder has been used, the tube needs a high temperature bakeout with an opening in the glass tube for air to escape in order to thoroughly burn out the binder before the tube is used. If a small-particle phosphor is used, simply drying the tube of the alcohol vehicle will suffice. Pouring liquid phosphor directly into a lamp can also give interesting streaks of color. Using heavily thinned phosphors can, by turning and twisting of the glass, direct streams of color to trail throughout the lamp.
- Airbrushing: (Warning, this must only be done in a thoroughly ventilated area, preferably in a chemical hood.) A slurry of phosphor and liquid binder or alcohol can be airbrushed onto parts before assembly into the final piece. Again, bakeout may be necessary to remove binders before use. Airbrushing with small-particle phosphors need only have an alcohol vehicle for application and evaporation usually removes it. Spray coating gives the best-controlled and brightest coating.
- Brushing: A small amount of phosphor is mixed with a vehicle of isopropyl alcohol and applied with a brush. This can yield a painterly quality to the phosphor application. Objects should be painted with phosphors under a short-wave UV lamp so the artist can see the true colors, as most phosphors appear uniformly white in ambient light.
- Screen printing: Patterns of phosphor colors can be applied on flat or curved plates using premade silk screens or stencils. The phosphor should be mixed with a liquid binder suitable for screen printing, which can subsequently be cleanly burned off during processing.
- Use of sandblasted masks: Designs can be applied to glass by sandblasting through a stencil, applying the phosphor to the sandblasted glass area, and wiping lightly, leaving the phosphor deposited solely in the sandblasted portions.
- Mixing with sand: Clean sand or small glass beads can be mixed with a small amount of phosphor and poured into tubes and agitated until the interior surfaces are uniformly coated with phosphor. With this method, the adhesion of the phosphor is better if finer milled phosphor is used. Since the sand is heavier and coarser than the phosphor, when poured out it leaves solely a light phosphor coating behind. Residual clean sand is fairly inert after tube processing and won’t affect the gas purity.
- “Explosive” coating: This is a technique by which powdered phosphor is “explosively” blown into the tube by utilizing vacuum. To coat a plasma piece, the tube must be evacuated through a tubulation equipped with a blown glass trap in, which a small amount of phosphor is placed. The tube is evacuated down to a rough vacuum and then the tubulation is sealed close to the pump, leaving the trap connected to the sealed piece. The phosphor is then poured or shaken out of the trap into the tubulation. The end of the tubulation is then broken open and the rapid inrush of air distributes the lightweight powder throughout the tube. Wherever the air rushes it carries the phosphor powder. No binder is required, due to the Van der Waals force. The tube is then processed normally after this coating process.
- Electrophoretic or electrostatic coating: A variation of the method is to follow the explosive coating technique but to direct the phosphor powder to specific areas by using electrostatic attraction. To do this the phosphor particles must be charged, so a piece of metal tubing is placed between the art piece and the tubulation holding the phosphor. Additionally, a pattern of metal tape is placed on the outside of the glass piece in some desired pattern. One terminal of a high-voltage DC power supply is connected to the metal tube and the other to the metal tape and the power supply is energized. When the tubulation is broken and the powder moves through the metal tube it picks up a charge and is drawn to the oppositely charged taped areas due to electrostatic attraction.
*Note that phosphors should always be cleaned away from edges of the glass that are going to be sealed or otherwise flameworked. If the phosphor powder melts into the glass, it can prevent it from sealing thoroughly.
4. Are there any safety concerns to be aware of when working with phosphors?
Yes, take care to avoid breathing airborne dust from phosphor powders. Wear a properly rated respirator mask and eye protection, and work in a well ventilated area when mixing/grinding the dry phosphor powders.
Please contact us with any additional questions or concerns.